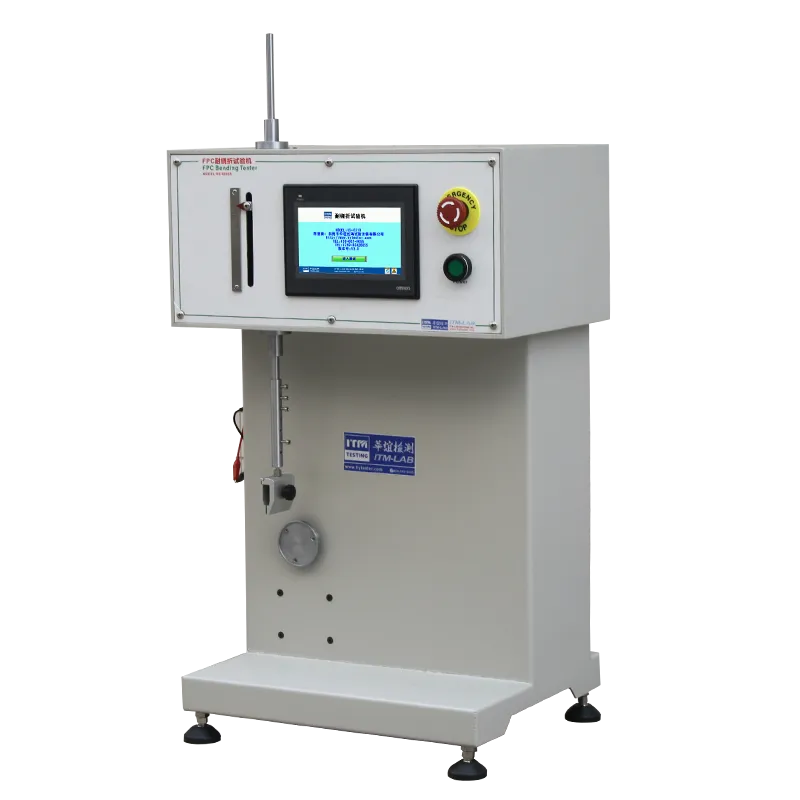
In today’s fast-paced industrial landscape, ensuring the longevity of electronic components is no longer optional—it‘s a necessity. Industrial electronics reliability testers bridge the gap between technical complexity and real-world application, offering solutions that are both scientifically rigorous and accessible to engineers and decision-makers. These systems simulate extreme operational scenarios, such as sudden temperature spikes or prolonged exposure to humidity, to predict how industrial electronics might behave over time. For example, a manufacturer using an Industrial electronics reliability tester could expose circuit boards to alternating cycles of heat and cold, mimicking decades of seasonal wear in a matter of days.
What makes these testers uniquely valuable is their dual focus on precision and usability. Advanced models may incorporate intuitive interfaces, allowing operators with varying technical expertise to configure tests for components like battery management systems or motor controllers. Simultaneously, built-in analytics tools could translate raw data into actionable insights, such as identifying a capacitor’s vulnerability to voltage fluctuations. This balance ensures that even non-specialists can leverage the technology to improve product design.
The relevance of industrial electronics reliability testers spans industries.
In aerospace, they might validate avionics systems against rapid pressure changes, while in consumer electronics, they may assess smartphone durability under repetitive mechanical stress. Modular designs further enhance adaptability; users can swap testing chambers or sensors to evaluate everything from high-voltage cables to IoT sensors, all within a single platform.
Beyond technical performance, these testers address broader industry trends. For instance, sustainability-driven manufacturers could use them to minimize material waste by pinpointing weak points early in R&D. Similarly, compliance teams might rely on testers to meet evolving standards like ISO 16750 for automotive electronics or ASTM D4169 for packaging durability. By aligning testing protocols with regulatory frameworks, businesses reduce risks of recalls or non-compliance penalties.