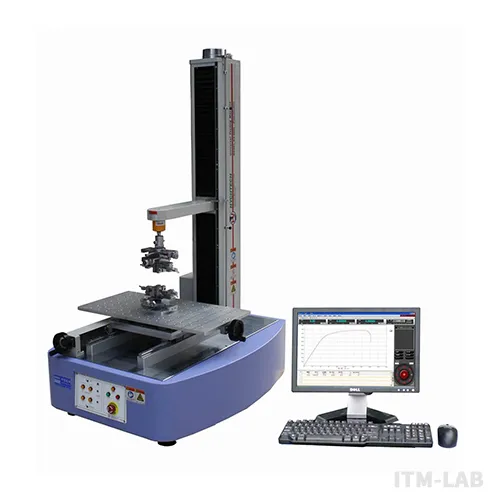
Introduction:The Critical Role of Precision in Quality Assurance
In industries ranging from automotive to medical devices, defects in materials or components could lead to costly recalls or safety risks. A mechanical tester, particularly a high-precision mechanical testing machine, serves as an indispensable tool for identifying weaknesses before products reach the market. By simulating real-world stresses and measuring responses with sub-1% error margins, these systems provide actionable data to optimize designs, reduce waste, and comply with international standards.
Key Features of Modern Mechanical Testers
1.Advanced Sensor Technology
Modern high-precision mechanical testing machines utilize ultra-sensitive load cells and strain gauges, akin to high-end laboratory scales but engineered for industrial environments. For example, ITM-LAB’s systems employ dynamic calibration to automatically compensate for temperature fluctuations, ensuring consistent accuracy even during prolonged tests.
2.Adaptive Control Systems
These testers may incorporate closed-loop feedback mechanisms to maintain preset parameters (e.g., 500N tensile force ±0.5%). Such precision could minimize human intervention, as seen in automated cable testing machines that detect insulation flaws or conductor breaks within seconds.
3.Modular Configurations
Like interchangeable Lego blocks, modular fixtures and software upgrades allow a single mechanical tester to handle diverse materials—from flexible polymers to rigid alloys. ITM-LAB’s universal testing machines, for instance, support fatigue, compression, and shear tests through swappable toolkits.
Industry Applications: Solving Real-World Challenges
1.Electronics Durability Testing: A high-precision mechanical testing machine could evaluate micro-USB ports over 10,000 insertion cycles, predicting wear patterns that might cause connectivity issues.
2.Medical Device Validation: Simulating physiological conditions (e.g., 37°C, 95% humidity), these systems test surgical sutures or artificial joints under biomimetic loads, ensuring compliance with ISO 13485 standards.
3.Automotive Safety Checks: By replicating decades of road vibrations in hours, testers identify fatigue cracks in brake components or seatbelt anchors, aligning with IATF 16949 protocols.
Why ITM-LAB’s Solutions Stand Out
ITM-LAB’s mechanical testers integrate features praised in recent Reddit discussions—multifunctionality, user-friendly interfaces, and robust after-sales support. Their environmental test chambers and battery test systems further complement reliability assessments, creating end-to-end quality control ecosystems.
Future Innovations: Smarter and Sustainable Testing
Emerging trends like AI-driven failure prediction could redefine electronics reliability testing by identifying latent defects early. ITM-LAB’s energy-efficient testing systems also align with sustainability goals, reducing energy consumption by up to 25%. Such advancements may enable manufacturers to stay ahead of regulatory demands and consumer expectations.
If you are interested in our products and want to discuss a purchase, please contact us.